Electric arc furnaces: the technology poised to make British steelmaking more sustainable

[ad_1]
In a move to embrace sustainable steelmaking, British Steel has unveiled a £1.25 billion plan to replace two blast furnaces at its Scunthorpe plant with electric arc furnaces. This follows the UK government’s commitment in September to invest up to £500 million towards an electric arc furnace at Tata Steel’s Port Talbot plant in south Wales.
This method of steelmaking can use up to 100% scrap steel as its raw material, resulting in a significant reduction in carbon emissions. It is the future of steelmaking.
Steel is an incredible material and for good reason. It’s the world’s most commonly used metal because it’s strong, durable and recyclable, making it the perfect material for everything from skyscrapers to electric vehicles and solar panels. More than 1.8 billion tonnes of crude steel were produced globally last year. That number is only expected to grow as the world transitions to a more sustainable future.
The UK uses around 12 million tonnes of steel each year. And in 2022, it produced just under 6 million tonnes, contributing to around 2.4% of the country’s greenhouse gas emissions.
Electric arc furnaces
There are two main steel production methods. Currently, Port Talbot and Scunthorpe use the blast furnace-basic oxygen furnace method. The purpose of the blast furnace is to separate iron ore extracted from the ground into its component parts: iron and oxygen.
A form of carbon, normally coal, combines with the oxygen in the iron ore. The outputs of this process are iron and carbon dioxide. The basic oxygen furnace is then used to convert the iron into steel.
As a global average, this method of steelmaking emits around 2.32 tonnes of CO₂ per tonne of steel produced.
An electric arc furnace works by generating a high-temperature arc between graphite electrodes, using electricity as the energy source. This arc is then used to melt metal inside a chamber.
Using this method, up to 100% scrap steel can be used as the raw material, while the blast furnace-basic oxygen furnace method can only use a maximum of 30% scrap. A switch to the electric arc furnace method could reduce emissions to 0.67 tonnes of CO₂ per tonne of steel produced when using 100% scrap steel.
In the future, it is also possible the electricity needed for electric arc furnace processes could come from 100% renewable sources, whereas a form of carbon will always be needed to reduce iron ore when using the blast furnace method.
Recycled steel
Steel is the most recycled material in the world, and so scrap steel is quickly becoming a crucial raw material. In 2021, the global steel industry recycled around 680 million tonnes of scrap steel. This equates to savings of almost 1 billion tonnes of CO₂ emissions, compared to using virgin steel production.
In 2021, more than 8.2 million tonnes of steel scrap was exported from the UK. If collected and sorted more carefully, using this material domestically could provide both environmental and economic value, by helping to meet growing national demand for steel.
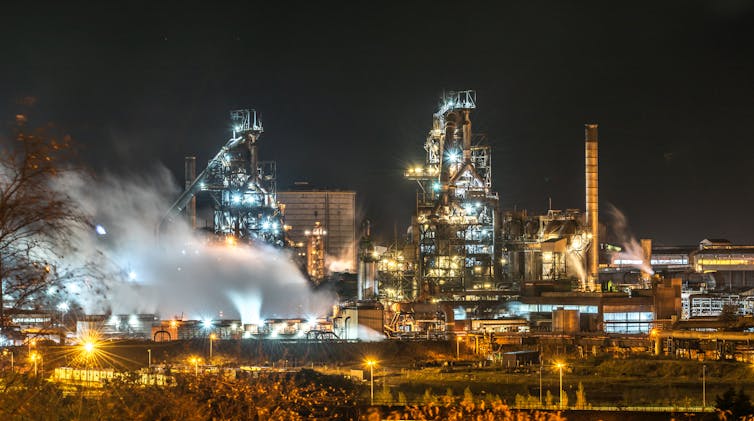
Christopher Willans/Shutterstock
We know that steel produced with an electric arc furnace can have different properties to blast furnace produced material. A large factor in this is the quality of scrap steel used in the electric arc furnace – if the scrap steel quality is low, then so will the quality of the output.
With that in mind, there is a need for research, innovation and skills development to ensure this transition to lower-carbon steelmaking methods is successful.
Finding and sorting the right types of scrap material, confirming material properties and increasing supply chain understanding of electric arc furnace steelmaking are all necessary for a wide range of steel products to continue to be made in the UK.
Sustainable steelmaking
There is a race across Europe to secure investment for sustainable steelmaking technologies. Hybrit is a fossil-free steel project in Sweden between several major steel producers and is already underway.
This follows plans to invest almost €40 billion (almost £35 billion) in low-emission steelmaking technologies over the next 20 years. Also in Sweden, the company H2 Green Steel has secured €3.5 billion (£3 billion) to build a hydrogen-powered steel plant.
In July 2023, the German government announced €2 billion (£1.7 billion) of support for Thyssenkrupp, the steel multinational. And that was on top of the €3 billion (£2.6 billion) it had previously announced to support the country’s industrial green transition. A
ArcelorMittal, the second largest steel producer in the world, has also announced green investment in their plants in Belgium and Spain, totalling more than €1.2 billion (£1.5 billion).
While the UK government has no published industrial strategy, other organisations have produced roadmaps for decarbonised steelmaking in the UK.
A report by the Energy Transitions Commission, a global coalition of energy leaders committed to net-zero emissions, outlined plans for investing in low-emission steelmaking in early 2023. With the right level of government and private sector investment, the UK could become a world leader in green steelmaking – but only it acts now.
As global temperatures continue to rise and the climate emergency deepens, the need for a decarbonised steel industry is greater than ever. Lower carbon methods of steel production are the future of the industry both in the UK and around the world.
[ad_2]