Why Ontario’s automotive workforce needs a boost to be ready for the EV boom | CBC News

[ad_1]
Ontario’s automotive industry is facing a range of hurdles that need to be overcome to be ready to supply the growing electric vehicle (EV) market and train the next generation of workers, workforce development specialists say.
The market is set to bring approximately 6,000 direct jobs to southwestern Ontario’s vehicle manufacturing plants, plus thousands of spinoff jobs.
Those jobs come as LG Energy Solution and Stellantis plan to build an EV battery plant in Windsor. Volkswagen is doing the same in St. Thomas, while General Motors has retooled the Ingersoll CAMI assembly plant. Stellantis is also rebuilding its Brampton and Windsor assembly plants.
“There are changes at almost every step in the process,” said John McNally, program director for clean and resilient growth at the Smart Prosperity Institute (SPI), which recently published a report that outlines hurdles the automotive sector will have to overcome. “These are good-news stories. It’s just that they have to be managed.”
The federal government announced on Dec. 19 that it would require all new vehicles sold in Canada to be zero emissions by 2035.
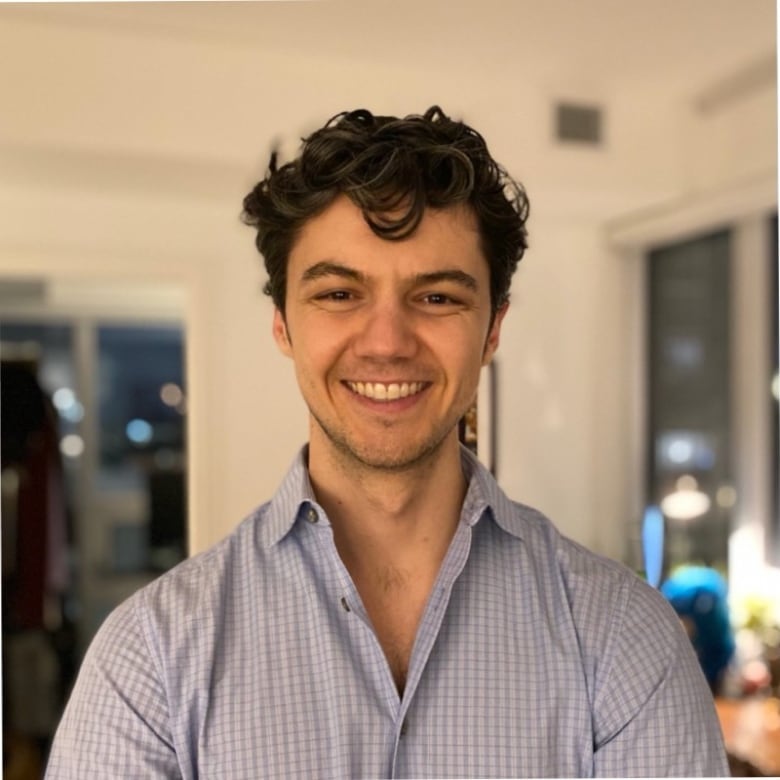
“We wanted to identify what the impacts of that major shift could be on workers by unpacking the supply chain that exists for electric vehicles. The technology is different here than it is for internal combustion engines,” said McNally.
He explained every company supplying the automotive sector will have to change. For example, technicians will need to familiarize themselves with the health and safety implications of working with a battery.
“But also, we need lighter and stronger steel, more semiconductors, more advanced software,” McNally said, noting some of the new skills won’t take long to retrain. Other jobs or tasks, he pointed out, don’t currently exist, but will be uncovered as the manufacturing process develops.
Wanted: Fast learners
At GM’s CAMI assembly plant in Ingersoll, retraining and rethinking the manufacturing process is already underway as the plants starts making the BrightDrop Zevo 600, an electric-powered delivery van.
A union head says workers are well versed in building frames and other components found on all vehicles, but they’ve needed to be trained on the production of the battery module. Some have travelled Detroit’s Factory Zero, the blueprint for GM’s other EV facilities.
“If you become a skilled tradesperson or you’re working our battery pair areas, for instance, there’ll be a higher, more involved training for working on the inside electrical components of the battery,” said Mike Van Boekel, chairperson for Unifor Local 88.
For others on the assembly line, training in battery safety and passing a standardized safety test have been enough.
“It’s to raise your awareness so you can understand what’s going on, how the batteries operate, how to work with them, where you can and can’t go on the floor,” Van Boekel said.
Time helps
In the area surrounding St. Thomas and London, where Volkswagen’s planned EV battery manufacturing plant is expected to bring 3,000 direct jobs and up to 30,000 offshoots when it starts production in 2027, time has been a valuable asset.
“We have a good time horizon. It’s almost four years, and the immediate need at the CAMI factory in Ingersoll is much less,” said Emilian Siman, executive director of the Elgin Middlesex Oxford Workforce Planning and Development Board.
“This gives us a chance to put forward some good training and educational programs to convert those interested in the industry and educators who are interested in teaching about it,” he said.
Still, there are pressing issues like a lack of transparency from manufacturers that need to be addressed moving forward, Siman said.
The next generation of workers
That lack of communication has been a challenge for post-secondary institutions as well, including Fanshawe College in London.
“Big companies need to come to Fanshawe and say, ‘Hey, listen, we want to make sure that you have this technology or your students who come out of your program are armed with this knowledge,'” said Carl Mendonca, associate dean of transportation technology, which sees an enrolment of roughly 1,700 students per year.
There have been some productive meetings with manufacturers that have allowed Fanshawe to adjust its curriculum to meet the needs of employers, but more are needed, Mendonca said.
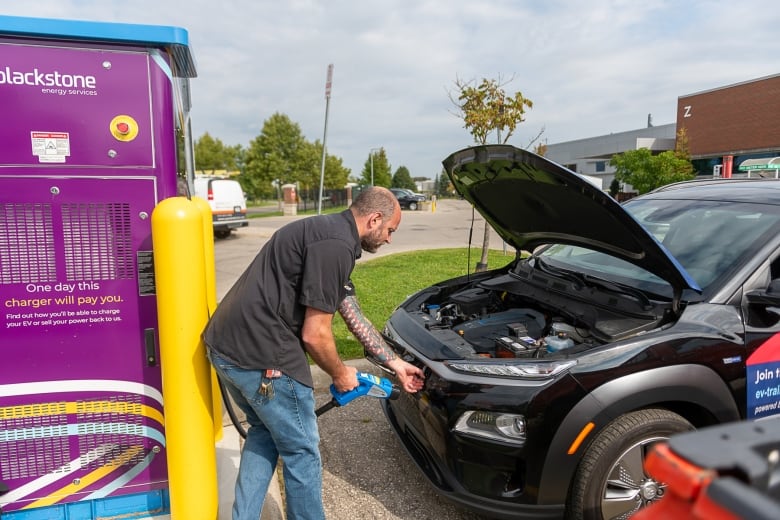
One example of Fanshawe’s contribution is its Green Vehicle Technology Program, which will include an in-depth look at electrical systems, charging infrastructure, EV design and alternative fuel systems, as well as a capstone project of building a working EV.
Fanshawe also offers free EV-sector courses in partnership with the Automotive Industry Association of Canada.
[ad_2]